Gibson モンタナファクトリー内部に潜入!
皆さん、こんにちは!G-CLUB SHIBUYA アコースティックギター担当のGibson大好き・石原です。
私、石原は 2024年8月に USA・モンタナ州ボーズマンにあるGibsonモンタナファクトリーを訪問してきました。三泊五日の弾丸ツアーでしたが、Gibsonアコースティックの事だけを考える贅沢な5日間。Gibson大好きな私にとってはまさに夢のような時間でした。
皆さんにはモンタナファクトリーツアーの様子を国内最速レポートいたします!
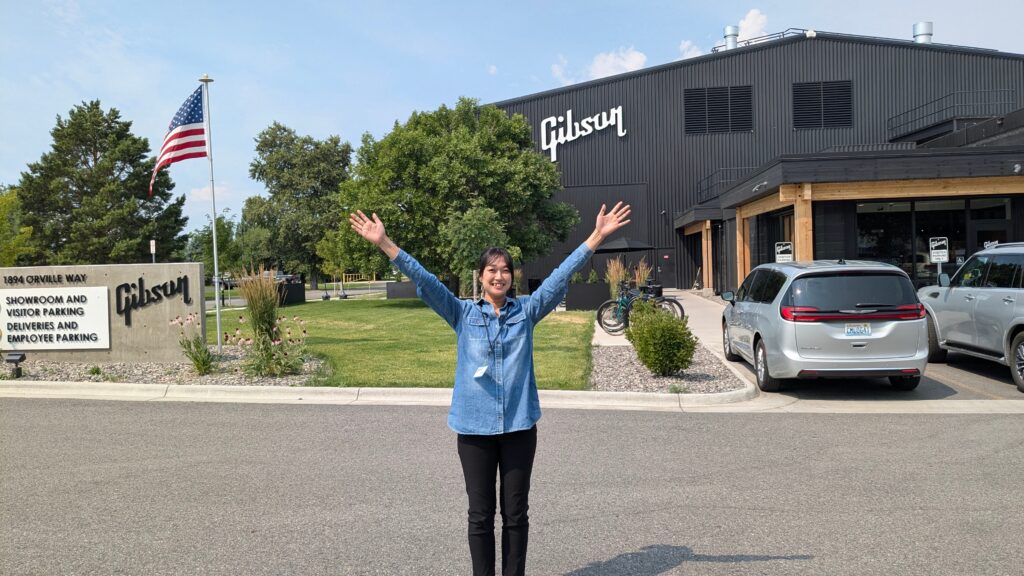
仕事でこの場所に来られるなんて…感無量です。
1989年からアコースティックギターの生産を開始したGibsonモンタナファクトリー。2022年には大規模な拡張工事を行い、約2倍の面積に生まれ変わりました!その内部はメディアへの公開が許されておりませんが、今回特別にファクトリー内部の画像をGibson Brands Japan様よりご提供いただきました。
Gibsonアコースティックが出来るまでの様子を順にご紹介しながら、『Gibsonサウンド』に欠かせない3つの秘密に迫っていきます!
到着してすぐに、ファクトリーツアーへGO!ファクトリー内部ではGibson アコースティック・プロダクト・スペシャリストのドン・ラファートさんが先導して、詳しく解説してくださいました。
Resaw エリア ~製材~
まず始めは入荷した木材を製材し、ギターに使用するトップ・サイド・バック、ネックの形にしていくResaw(リソー) エリア。全ての始まりとなるResawエリアはGibsonアコースティックの『要』です。
このエリアにはカラマズーやナッシュビルの工場からモンタナファクトリー移転時に持ち込んだマシンが多くあります。楽器の作りに大きな影響を及ぼす製材マシンやネックプレスマシン等は最新のものにはせず、歴代の工場で引き継がれてきたものを今でも使っています。
ここでびっくりするのが、モンタナファクトリーが開設された当時は『ログ』と言って丸太のまんまワイルドに木材が入荷していたそう。現在は効率化を図り、ある程度小さく製材された状態でResawエリアに入荷しています。
木材はキルン・ドライ(強制乾燥)をして、モイスチャー・コンテント(含水率)を整えた上で入荷しますが、その後少なくとも30日間はモンタナの気候に慣らしてからギターの製作に入ります。
トップ・バックのブックマッチは裏側から光を当てて、しっかりと隙間なく接着しているか確認。
大まかなネックのシェイピングやロゼッタインレイを埋め込むための溝彫りやサウンドホールの穴開けは、コンピューターによる数値制御で木材を加工するCNC(Computer Numerical Control)マシンで行います。
White Wood エリア ~組み上げ~
WhitewoodエリアではResawエリアで製材した材を組み上げて、いよいよ『箱』の形にしていきます。
モンタナファクトリーではボディサイドは『リブ』と呼ばれています。
浸水したサイド材を、高温のプレス機に5分ほどかけてボディサイドの『くびれ』を成形します。
Hummingbird/Dove、J-45、J-200、L-00など、モデルによってくびれ具合が異なるのでプレス機は一つではなく、各モデルのために用意されています。
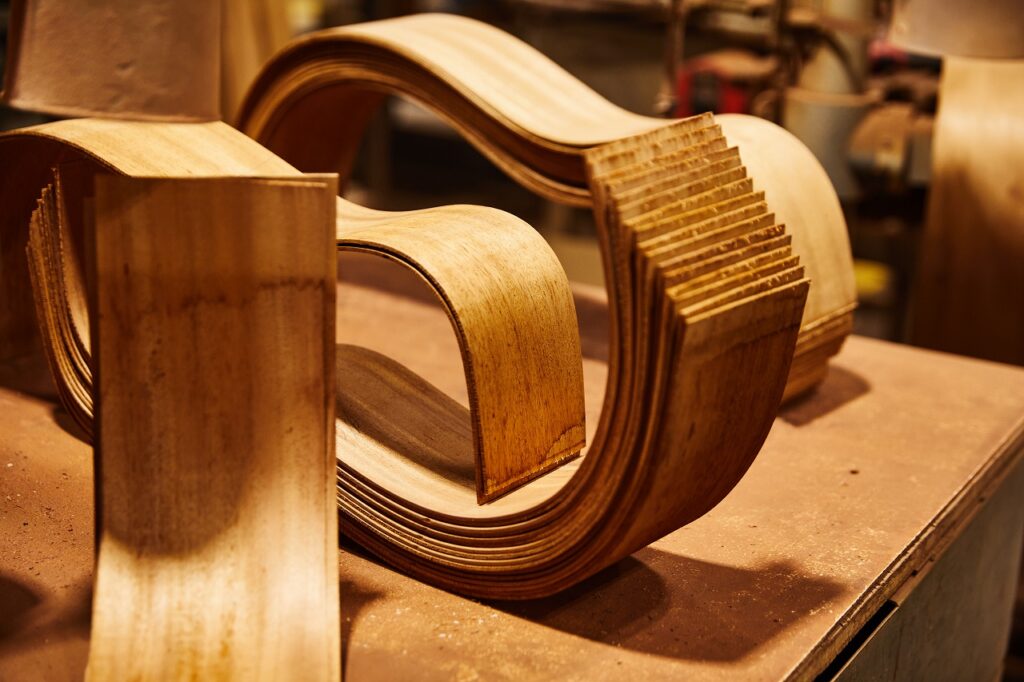
サイド材をプレス機で曲げたら、左右のサイド材同士を繋ぎ合わせ、ヘッドブロックとテールブロックを付けます。
ボディをモールドに入れて、トップとバックにカーフィング(ボディ内部の淵にある伸縮自在な蛇腹状のパーツ)を取り付けます。カーフィングにより、ボディトップとリブがしっかりと糊付けされます。
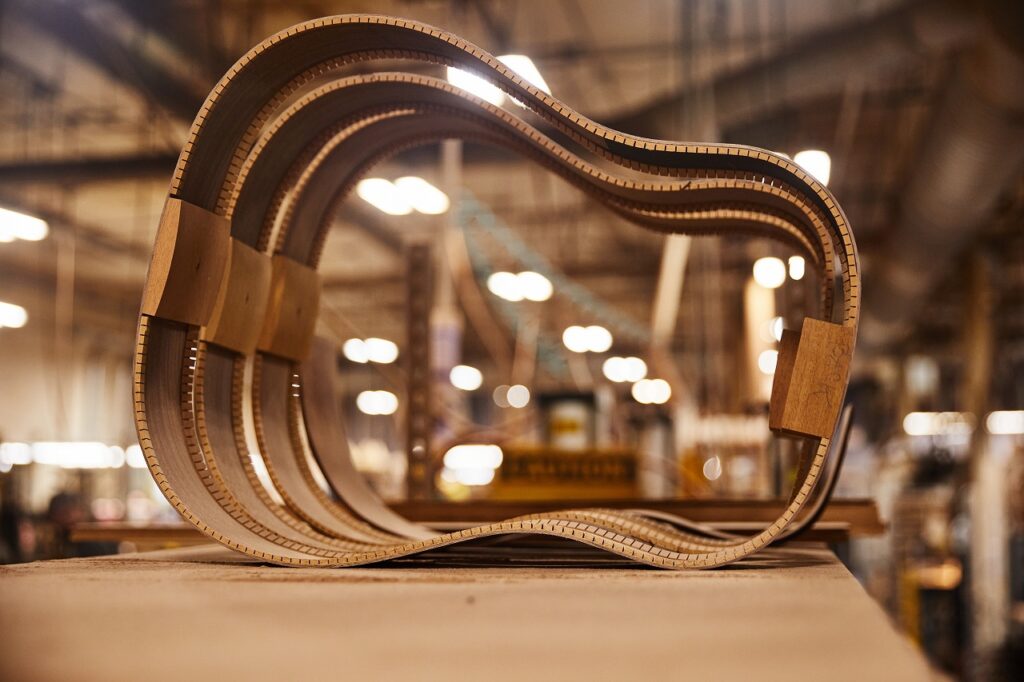
セミアコ等のアーチトップに対して、一般的なアコギは『フラットトップ』と言われますが、実はGibsonアコースティックのトップとバックは完全なる『フラット』ではありません。
え?そうなの?と思った方も、いるのではないでしょうか?
Gibsonアコースティックのトップは28Foot Radius、バックは12Foot Radiusの非常に緩やかなアーチを描いているんです。Gibsonアコースティックは価格に関わらず、同じようにこのドームド・トップ&バック構造となっています。皆さんも是非お持ちのGibsonアコギを横から見てみてください。トップもバックもゆる~くカーブしているはずですよ。
カーフィングを付けて左右のサイド材同士が繋がったら、次はトップとバックをくっつけて『箱』にしていきます。パラボリック・サンダー(放物線状の削り機)でサイド材の端面が目標のアールになるよう、サイド材の端面をやすり掛けします。
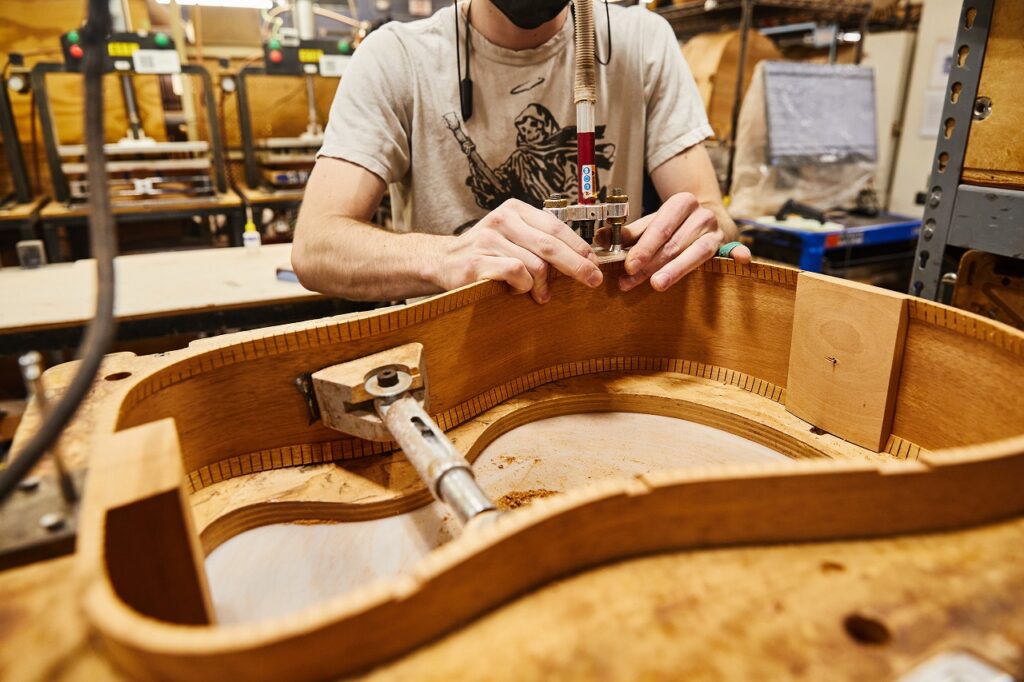
トップ、バックの裏に貼り付けるブレーシング材にも同じくアールを付けていきます。
トップ材自体を曲げてから接着するのではなく、アールを付けたブレーシングをトップとバックに接着することで自然にアーチを描くよう計算されています。この製法によりトップ材には常にテンションがかかっている状態になり、弾いた時に細かくバイブレーションするそう。
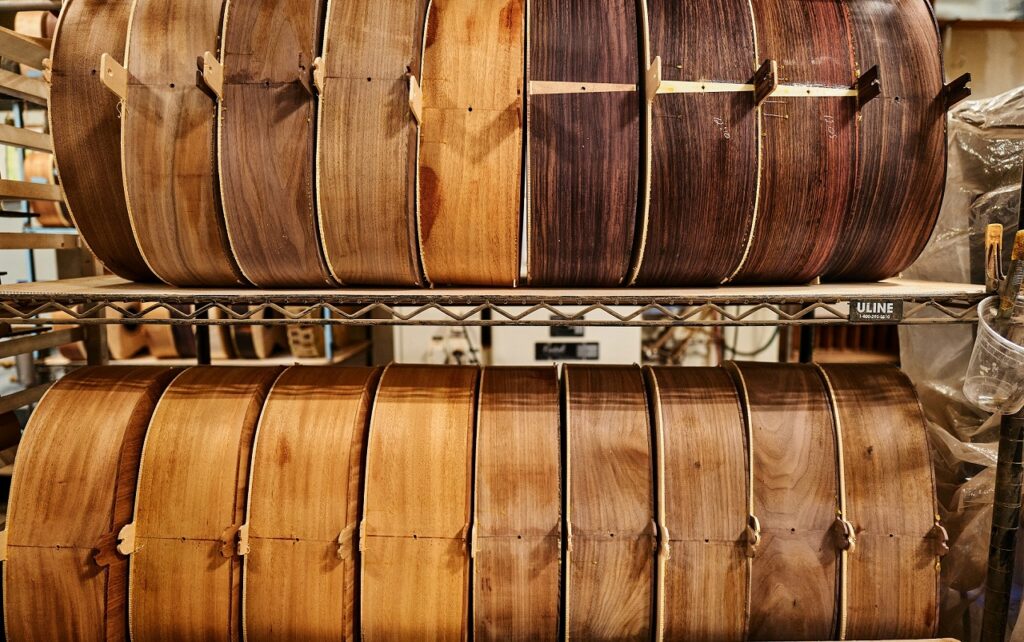
昔、ドームド・ボディではなく完全なる『フラット』なトップでデモ機を作ってみたら、ギブソンらしいサウンドが失われてしまったとか。『もちろん完全なフラットにしたら製作効率は上がるけど、このドームド・トップ&バックはGibsonサウンドに絶対に欠かせないポイント。今後も効率化せずに続けていくよ!』と、ドンさんは仰っていました。ダイナミックなGibsonサウンドの秘密がここにありました。
Gibsonサウンドの秘密 その①
ドームド・トップ&バック
箱になったボディにダヴテイル・ネック・ジョイント用の凹み溝を作り、ボディ外周にバインディングを巻きます。マスキングテープで補強して、バインディングの接着剤が乾くまで一晩置きます。
次はネック周りの作業に入っていきます。
ネックにトラスロッドを埋め込む溝を作り、トラスロッドを仕込みます。
トラスロッドの上には埋め木を入れて、その上から指板を貼ります。埋め木には硬質なメイプルを使用し、ネックの強度を保っています。
Gibsonアコースティックのヘッドはよ~く見ると3ピース構造になっています。
ネックからひと繋がりに延びるセンターピースの両側に『イヤー』という耳を付けています。
1ピースでヘッドシェイプの形に切り出さずに、両端にイヤーブロックを付けることで木材の無駄を無くしています。
CNCマシンを使って、ダブテイルジョイントの凸部の形成、ペグを取り付ける穴、インレイやフレットを埋め込むための溝を開けていきます。ヘッドのGibsonロゴインレイや指板のインレイは一つ一つ、手作業で埋め込んでいます。
フレットは専用の道具を使って2人の職人が手打ちしています。細い注射器でフレット溝に接着剤を流し込み、1本ずつ打ち込んでいました。フレットは機械制御で打ち込むメーカーもありますが、Gibsonでは手作業にこだわっています。指板材にも若干の硬さの違いがあるため、材を見て打ち込む回数や強さを変えているそうです。まさに経験が成す職人技です。
反面、ネックやボディの大まかなサンディング(やすり掛け)はコンピューター制御されたサンディング用のロボットが行っています。サンディングの作業は非常に体力を使う工程の一つです。大まかなサンディングは機械に任せることで、働き手の負担を軽減しています。その後のネックシェイプのサンディングや細かな部分、仕上げのサンディングは職人による手作業です。
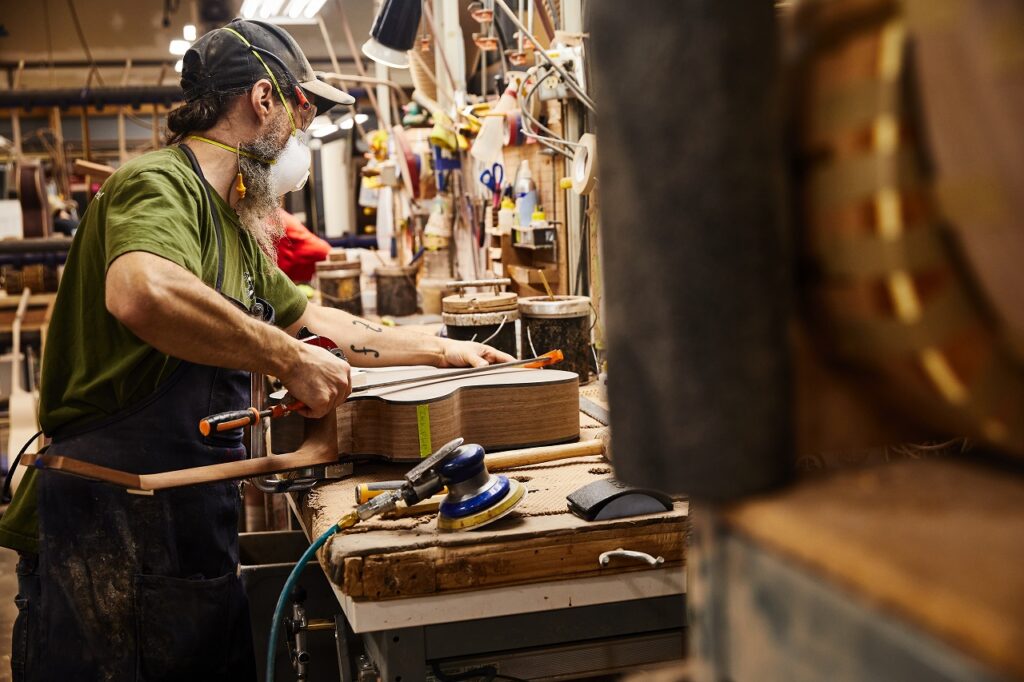
さて、ここまで来たらついにボディとネックをジョイントしていきます。ドンさん曰く、『このジョイントのパートがGibsonのギター作りにおいて最も重要な工程だ』とのこと。ボディとネックの接合には特に熟練の職人が携わっています。弦を張ってテンションがかかるとどうなるか、想像しながら作業しているそうです。
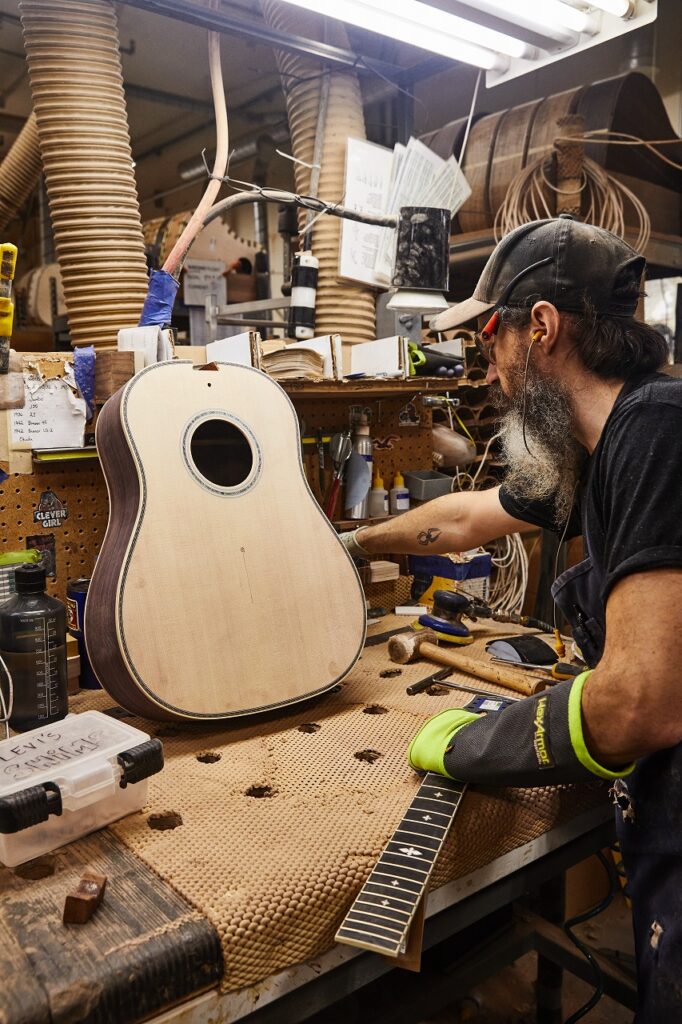
他のブランドではジョイントにスーパーグルーやタイトボンド等、化学系の接着剤を使用することが多いですが、Gibsonは違います。自然由来の『ハイドグルー(ニカワ)』で接着をしています。冷えると固まる性質のあるニカワは熱した状態で塗布する為、テクニックが必要です。
ニカワ接着のメリットとして、木材の中にニカワが沁み込んでいき、隔たりとなる『接着層』を残さないため、ボディの振動をダイレクトにネックへと伝えることが出来ます。
ニカワ接着のダヴテイル・ジョイントは手間はかかりますが、Gibsonサウンドを守っていくための大切なポリシーの一つです。
Gibsonサウンドの秘密 その②
ニカワ接着のダヴテイル・ジョイント
最終サンディングをして、ついに塗装前のギターが完成しました。次は塗装の工程に入っていきます。
Sprayエリア ~塗装~
Sprayエリアは2022年の改装で新しく整備されたエリアです。この大規模な改装により生産効率は大幅にアップし、一日の生産台数は平均75本から最高200本にまで伸びたそうです。
ここからのエリアではベルトコンベアで吊り下げられた沢山のギターが各パートを流れていきます。
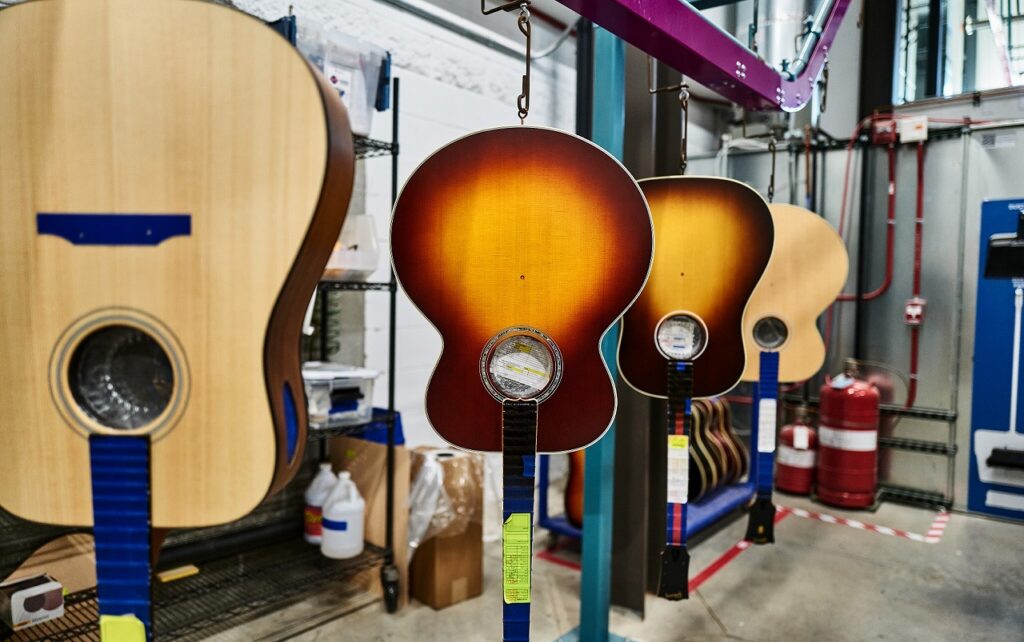
塗装前のボディにフィラー(目止め材)を塗り込みます。ハケでフィラーを塗り、布でゴシゴシ。このパートも完全なる手作業です。このフィラー工程では、木材の導管を埋めて凹凸感をなくし、この後に行うラッカー塗装をしやすくするとともに、ボディに大まかな色付けをする役割も担っています。マホガニー、ローズウッド、スプルース等、材の色味に合わせたフィラーが使用されています。
フィラーの次はGibsonのアイコンでもあるサンバースト・フィニッシュをハンドスプレーで吹いていきます。ギターの『顔つき』を決めるこの工程は熟練工が担っているそう。
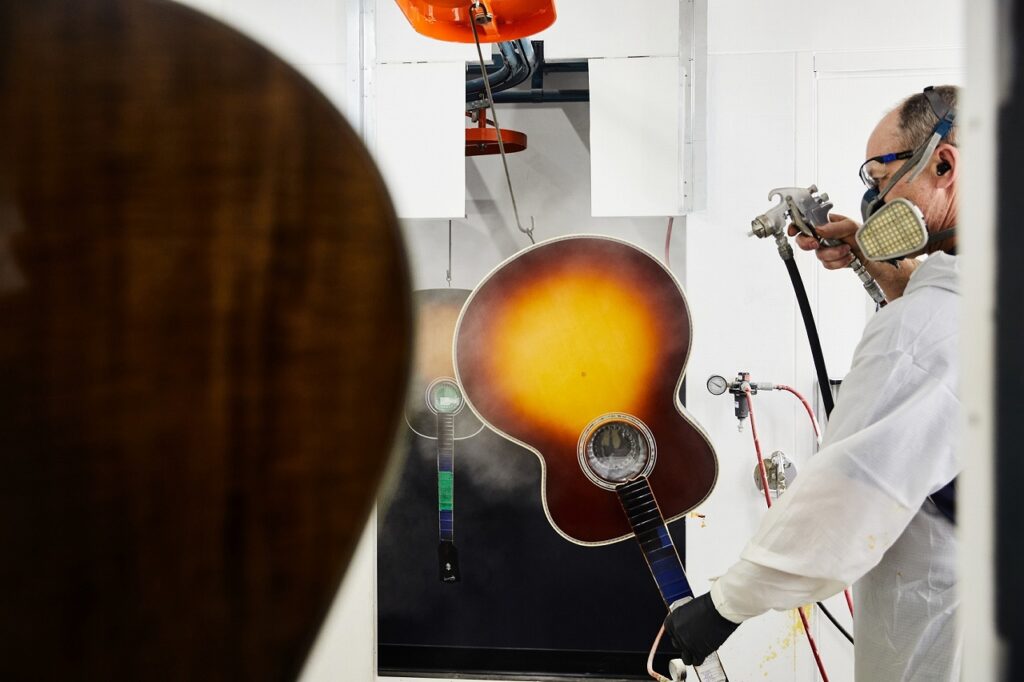
スプレーでサンバーストを吹き付けると、白いバインディングの上にもカラーが乗っかってしまいますよね?安心してください。ギターはハンド・スクレイプ・エリアに運ばれます。
ここでは、バインディングの上に乗っかった塗膜を手作業で取り除いています。このパートでは細やかな作業が求められるためか、職人の中で女性の比率が多かったです。プレパラート(顕微鏡で見たいものを載せるガラスのプレート)を使って削っている職人もいましたよ。
カラースプレーが終わったら、仕上げのクリアラッカーを吹いていきます。仕上げ、と言ってもここからが長いんです。
全てのGibsonアコースティックにはニトロセルロース・ラッカーを使用しています。
ラッカーを7回塗布してから、1日寝かせて乾燥、最後のクリアコートを2回塗布して再び乾燥させます。
3日ほど寝かせて乾いたら、バフ掛けをしてさらに艶出しをしていきます。
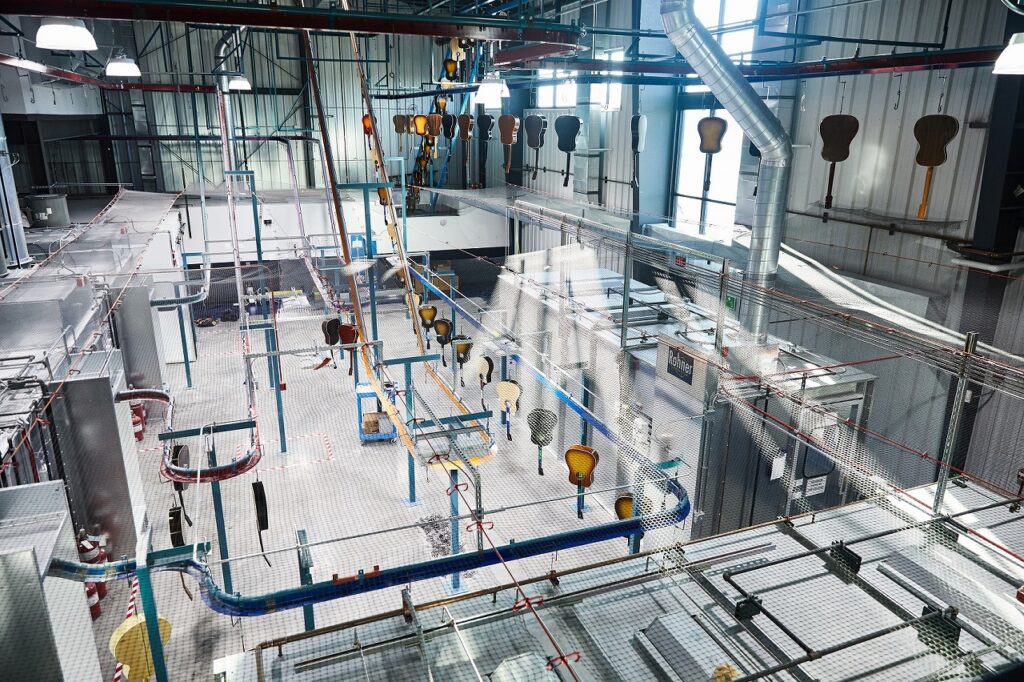
Gibsonアコースティックの場合、1本のギターの塗装が完了するまでに10日から14日は掛かります。
ラッカー塗装は手間が掛かりますが、ポリウレタンやポリエステル等の化学的な塗装よりも塗膜を薄くすることが出来ます。薄いラッカー塗装がGibsonらしい『素直な鳴り』に繋がっています。
さらに、ラッカー塗装は年を追うごとにラッカーの中に含まれている溶剤や余分な水分が揮発していくため、塗膜がさらに薄くなっていきます。ヴィンテージのGibsonを見てみると確かに塗膜が薄くなり、杢目の凹凸感を感じられる個体がありますよね。新品の状態から年々サウンドが変化していくのは、ラッカー塗装のGibsonだからこそ、より味わえるというわけです。
Gibsonサウンドの秘密 その③
ニトロセルロース・ラッカー塗装
Final Assemblyエリア ~パーツ取り付け・最終点検~
ここまでバトンを繋ぎ、最後の工程を担うのはFinal Assemblyエリアです。このエリアも2022年の改装で新設されました。ここではパーツの取り付けから、ウエットサンディング(水研ぎ)、バフ掛け、最終点検、箱詰めまでが行われます。
まず、塗装されたギターにブリッジを接着し、全体をバフ掛けします。
その後、ギターを『PLEK』にかけます。『PLEK』とは楽器のネックおよび指板、フレット等の状態を1/1000インチ単位で数値化、可視化できるマシンです。モンタナファクトリーでは2014年に導入されました。
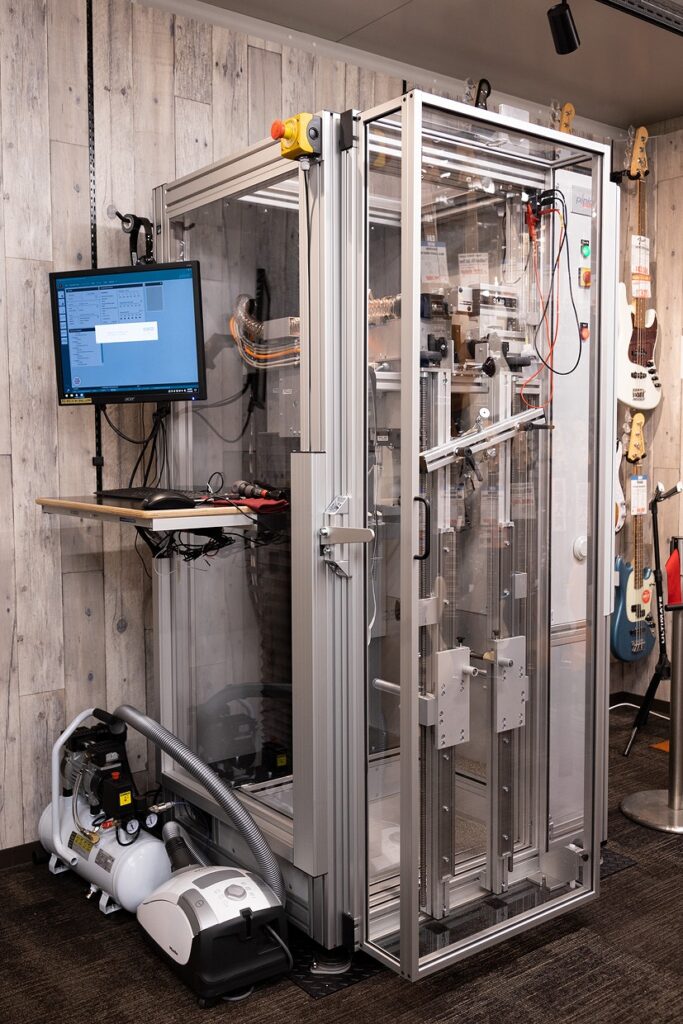
ペグやナット&サドル、ピックアップ、ピックガード等のパーツを順番に取り付けていきます。各パートごとに工程表があり、抜けが無いようになっています。
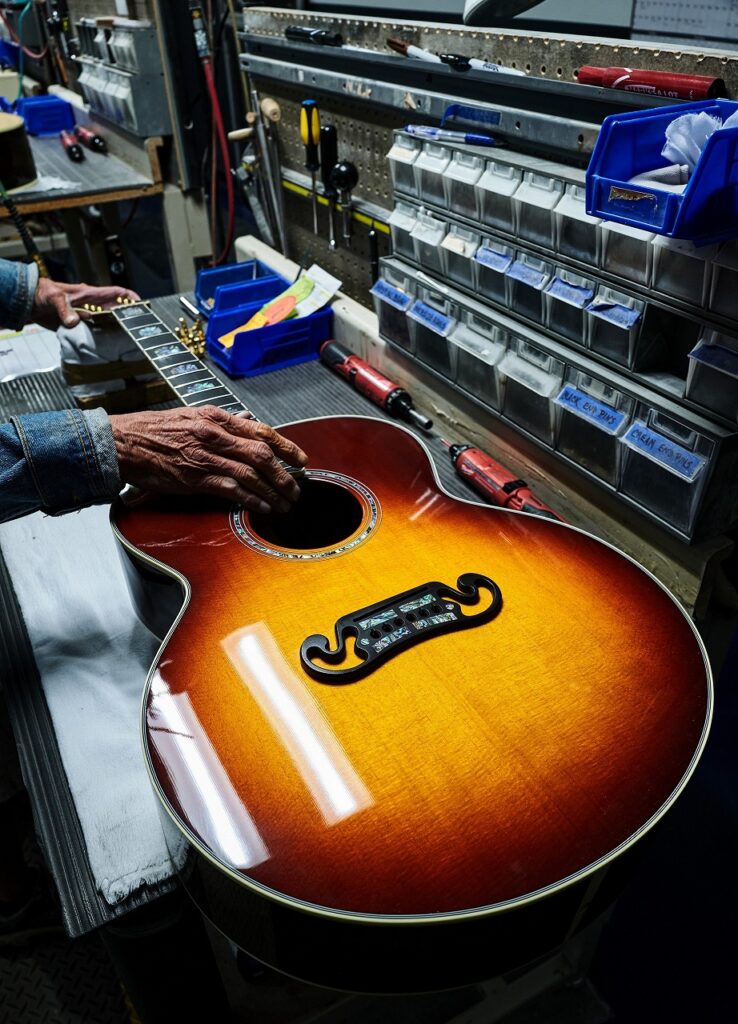
最後に、弦高やバフ掛けの精度等も厳しくチェック。もし不具合があった場合は、各エリアに戻して作業をやり直します。
Final AssemblyエリアはGibsonアコースティックが出荷される前の『最後の砦』でもある為、ここを担当する職人は自身もギタープレイヤーであることが求められているそう。すべてのフレットで問題がないか、実際に弾いて確かめる姿も見られました。
完成したギターは箱詰めされて、全世界のディーラーの元へと出荷されます。
Gibsonギターがついに完成!
Gibsonサウンドを生み出す3つの秘密
その① ドームド・トップ&バック
その② ニカワ接着のダヴテイル・ジョイント
その③ ニトロセルロース・ラッカー塗装
Gibsonギターが出来るまでの工程、そしてGibsonサウンドを生み出す『3つの秘密』を解き明かしてきました。作業効率よりもサウンドを重視するGibsonのポリシー、お分かりいただけましたでしょうか?深く知ることで、Gibsonの音色もより良く聞こえてきますよね!
今回のモンタナファクトリー訪問で 私、石原はGibsonアコースティックの『サーティファイド・スペシャリスト』に認定されました。今回の訪問で得た知識を店頭でも皆さまにお届けいたします。
このブログの中には書き切れていないことが沢山ありますので、是非『Gibson談義』いたしましょう!
Gibsonアコースティックにご興味を持っていただけた方は、G-CLUB SHIBUYAまでお気軽にご相談くださいませ。
最後までご覧いただき、誠にありがとうございます。G-CLUB SHIBUYAのGibson大好き・石原でした!
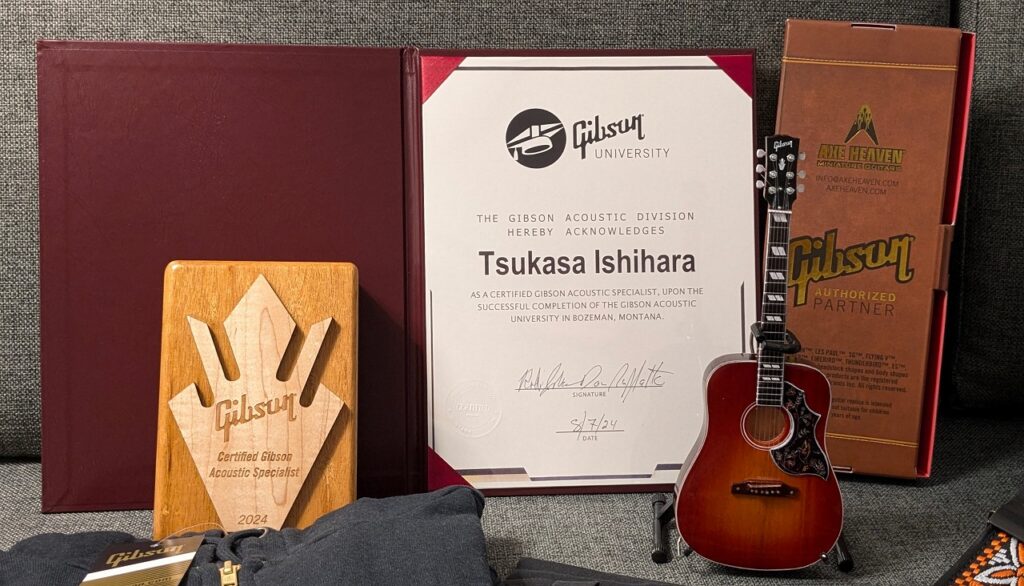
名前入りの『サーティファイド・スペシャリスト』認定証をいただきました。
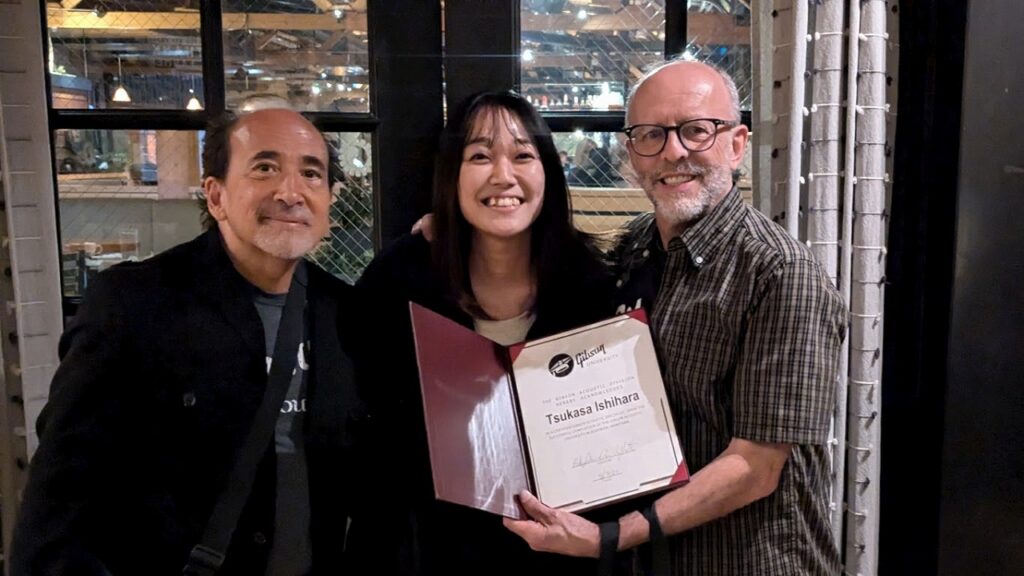
そして嬉しそうな石原。